2300 Market Construction Reaches New Heights
New construction photos of 2300 Market reveal exciting progress on the 8-story, 225,000-square-foot life science research and discovery building.
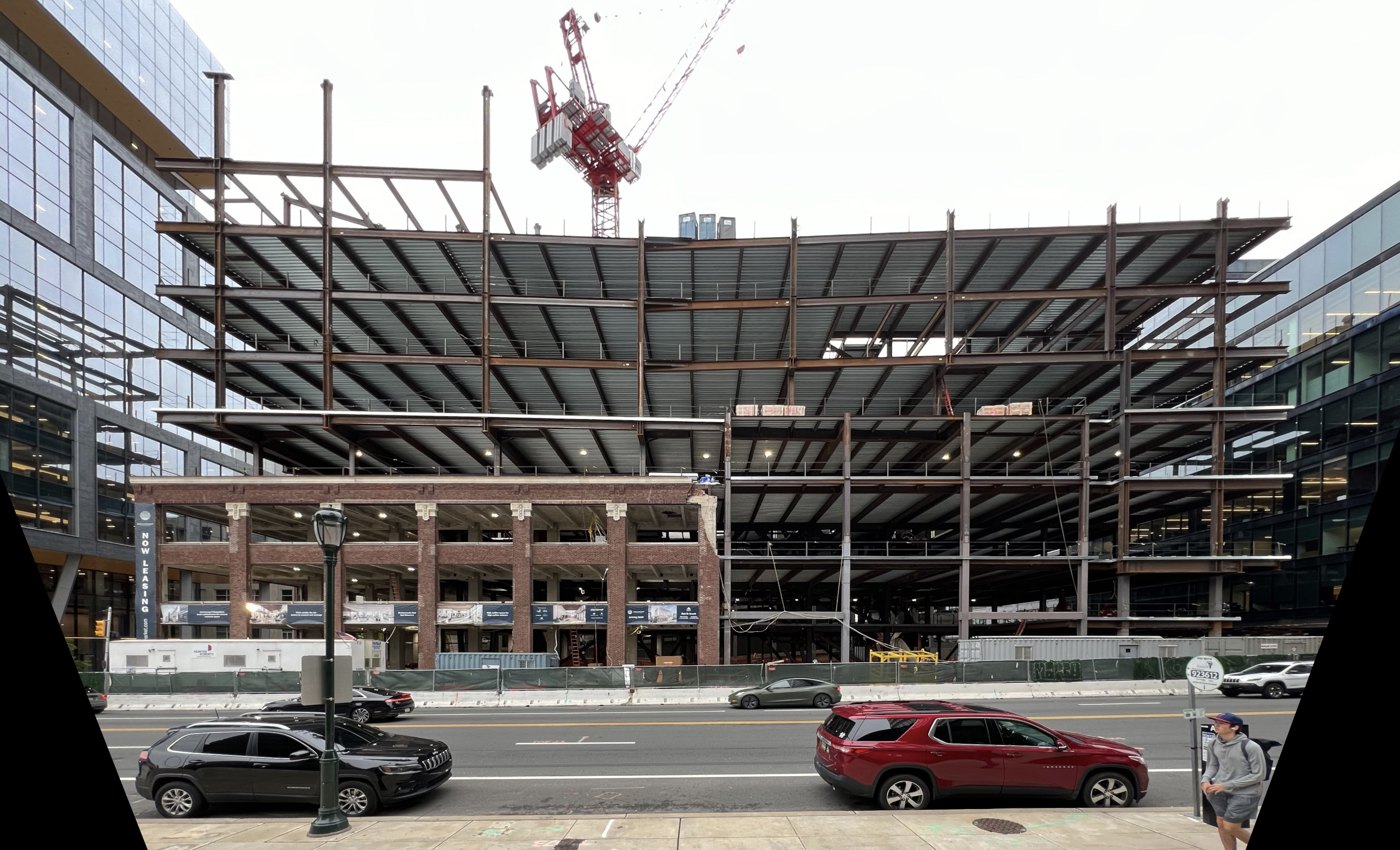
New construction photos of 2300 Market reveal exciting progress on the 8-story, 225,000-square-foot life science research and discovery building.
The new Penn's Landing Park is scheduled to break ground on September 6. The 11.5-acre park will reconnect Philadelphia to the Delaware River, guiding pedestrians from city sidewalks to a new public landscape, amenities, and attractions that bridges over I-95.
KieranTimberlake's scope of work includes the architectural design of the central pavilion which will house and support park amenities, including a café, skate rentals and support for the adjacent ice rink/summer plaza, and office space for the Delaware River Waterfront Corporation (DRWC) park operations team. It is projected to be Philadelphia's first mass timber and zero carbon structure for public use.
Since 2018, KieranTimberlake has partnered with UNICEF, GerHub, Arc'teryx, The North Face, the University of Pennsylvania, and others to reimagine the traditional Mongolian ger in order to find low-cost, high-value solutions for decreasing coal consumption and improving indoor air quality in the capital city of Ulaanbaatar.
We began by working closely with Mongolian communities to better understand how they kept their homes warm and improved their gers' thermal performance during brutal winters—the city is the world's coldest capital and regularly sees temperatures below -40 ºC. Five families allowed us to collect thermal data on their homes over the winter, providing our team with valuable insights into real-life fuel use and building performance.
In an op-ed published in Fast Company magazine's Co.Design blog, titled “Should We Save Mid-Century Modern Icons That Hurt The Environment?” partner James Timberlake outlines an ethical approach to the energy efficiency problems that plague mid-century modern architecture.
Nearly thirty million commercial buildings were constructed after World War II in the period often referred to as the golden era of building, long before our modern understanding of carbon emissions and the human impact on global warming. Buildings are responsible for at least 30% of greenhouse gases. What happens when some of those structures are beloved architectural icons, designed by architects like Mies van der Rohe, Eero Saarinen, and I.M. Pei?
Timberlake says that creative and unconventional thinking is needed to preserve important works of mid-century architecture while bringing them to energy code compliance or better. A few solutions include rethinking curtain walls, using life-cycle inventory data sets to analyze the environmental impact of building materials, and reusing existing facades while finding additional ways to improve efficiency. "The current tools at our disposal allow us a better way forward," Timberlake writes, concluding that "the impact of historical architecture infrastructure on the energy crisis is an ethical problem that we can no longer afford to ignore."
Last week at the climate talks in Paris, world leaders committed a full day to discussing public policies and financial solutions to reduce carbon emissions within the building sector. It's widely documented that buildings are the culprit for at least 30% of global greenhouse gas emissions. Meanwhile in the building sector, there's an ongoing discussion about what to do with inefficient buildings from past eras. Debate around historic value versus economics inevitably leads to the big question: Are these buildings worth retrofitting, or do we tear them down and start over?
Ground broke on Brown University's new School of Engineering research facility last month. The new four story building will create 20 new cutting-edge laboratory modules, including two specialized nanoscale and biomedical engineering laboratories, and will add 80,000 square feet of space. The addition comes at a good time for the School of Engineering, which expects to see its number of undergraduate students double between 2007 and 2017. The new facility will be able to house 15 faculty members, approximately 20 research associates, 80 graduate students, and a large number of undergraduate students.
Read MoreThe Consortium for Building Energy Innovation (CBEI)—formerly the Energy Efficient Buildings Hub—at the Philadelphia Navy Yard is a research initiative funded by the Department of Energy and led by Penn State University that seeks to reduce the energy usage of commercial buildings 20% by 2020.
At the retrofit project at Building 661, known as the Center for Building Energy Science and Engineering, work is almost complete on the comprehensive transformation of the former Navy recreational building (unoccupied since the late 1990s) into a facility that will welcome the public and educate visitors about energy-efficient building practices. Staff and researchers have begun moving into the workroom and offices. The ICon visualization lab—dedicated to facilitating the use of virtual reality techniques in design, construction, and other disciplines—has been installed, and the telepresence room recently held its inaugural Building Steering Committee session. During the renovation process, the exterior envelope of the building was completely refurbished, and large expanses of new glazing were introduced in concert with a pair of new and retrofitted skylights to suffuse the workroom interior with natural daylight, reducing lighting usage and energy loads. Per the CBEI mission, all building systems are completely visible, including the main mechanical room, passive and active chilled beams, a low velocity underfloor system, and a split system in offices. Installation of landscape, punch listing, and commissioning should be complete by the end of the year.
Topping off the structural steel at Congregation Rodeph Shalom was celebrated last week with a ceremonial signing of the highest steel beam by members of the clergy and administration, congregants, and representatives from the construction manager and the KieranTimberlake design team. The beam was hoisted into place by Intech Construction the following morning. In the coming weeks, concrete slabs will be poured for the first and second floors, and infill between the existing building and the new addition will continue.
The Consortium for Building Energy Innovation (CBEI)—formerly the Energy Efficient Buildings Hub—at Philadelphia's Navy Yard is a research initiative funded by the Department of Energy and led by Penn State University that seeks to reduce the energy usage of commercial buildings 20% by 2020. We are currently undertaking the retrofitting of a 1940s recreational facility for CBEI's headquarters, along with the construction of a new classroom building across the street. Both projects aim to be completed by mid-summer of 2014.
Over the past month, structural steel was erected for the classroom building, known as the Center for Building Energy Education and Innovation, revealing the form the eventual building will take. In keeping with the industrial character of the Navy Yard, the structural steel is left exposed in many of the building's public spaces, making the erection of the steel a critical milestone for the project. Now that the steel is in place, a second floor concrete slab can be poured and work on the exterior façade can begin.
An important aspect of environmental sustainability is the careful management of construction waste through recycling or landfill diversion. Normally, the contractor specifies a waste management company responsible for dumpsters on site, transportation, sorting, processing, landfill diversion, and accounting. In order to ensure that design and construction methods efficiently integrate with the processing of construction waste, KieranTimberlake recently made a visit to a local waste recycling and recovery facility.
Richard S. Burns & Company Inc. is a family-owned business that has been in operation for over 40 years. The company pioneered landfill diversion techniques long before the practice was commonplace because of its ability to monetize the recycling streams. It operates a 10-acre facility in North Philadelphia and employs many individuals in the surrounding community.
Our visit helped us understand what happens once waste leaves the construction site and allowed us to see first-hand how it is repurposed into a variety of recycling streams, often achieving a landfill diversion rate of 99%.
Last week, while the city slept, the first above-ground structure emerged at Dilworth Plaza with the installation of steel columns and edge beams that will form the new cafe and stair headhouse on the northern end of the plaza. Until now, work has been concentrated below ground in the new transit concourse and on the plaza level, largely out of view of passersby. But on Wednesday evening, January 29, after most of the traffic had dissipated at Philadelphia's City Hall, a 300-ton crane and several trucks bearing shop-fabricated steel pieces arrived to begin the installation.
Read More