Testing Steel Finishes for Aesthetics and Sustainability
Steel-clad walls surround a new elevator inserted in the narthex in Houghton Memorial Chapel at Wellesley College.
© Halkin Photography LLC
Peter Curry, manager of our fabrication studio, undertook a study of steel finishes related to our work at the Multifaith Center at Wellesley College.
We initiated a study to explore different methods for producing a durable, environmentally friendly, and cost-effective finish for steel fabrications in an interior environment. Our aesthetic goals included challenging the traditional notion of what constitutes a “blackened” finish by testing alternative mechanical and coating finishes in combinations that can be easily reproduced.
Traditional steel blackeners were too toxic for the environmental sustainability goals set for the new Multifaith Center at Wellesley College. Alternative finishes include non-acidic steel patinas formulated from dye-oxides, tinted metal sealing waxes that are applied hot or cold, a series of lacquers and clear coat paints/sealants, and linseed oil. These different categories of finishes were tested in combination except for lacquers with waxes since both of these are final top-coat sealants for metal.
The finished steel fabrications at the Wellesley Multifaith Center will be made from hot-rolled steel profiles. Traditionally, steel blackeners are applied to cold-rolled steel because its surface is raw and unprotected; therefore, chemical reactions incited by blackeners and patinas occur instantaneously on application. In consequence of this, the project determined to focus on hot-rolled steel both for its aesthetic qualities and the protective properties of its mill scale. The decision to express the rawness of hot-rolled mill scale as a finish then placed special emphasis on finding a clear top-coat that would preserve the desired finish and be durable in the field.
Surface preparation is a critical part of the finishing process to cleanse the material of dirt that could undermine the integrity and quality of the finish and to provide a desired aesthetic effect. A fine Scotch-Brite pad was used to prepare the steel for top-coating. This manual process was selected over other mechanical processes because its finished appearance is even; it creates a "machined" look. The project tested all finishes on both hot-rolled sheet steel and hot-rolled stock (1/4" x 2"). As noted previously, the sheet was mechanically prepared for finishing; the stock in this test was not. The samples of stock we acquired were clean and even enough that only solvent cleansing was necessary. However, on some of the patina samples the stock was sanded to help the patina knit to the surface.
Testing Finishes
Patinas
All patinas used are manufactured by Ron Young of Sculpt Nouveau. They were chosen because of the simplicity of their application and because each series of patina available offers a different chemical composition, both acidic and water based. A "patina stain," which is a concentrated form of the dye-oxides that tint the patina products, was also tested.
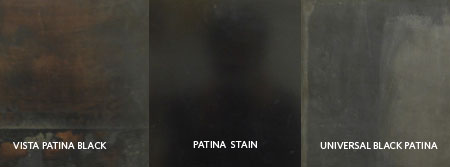
Patinas
1) The Vista Patina Black was the only acidic patina that was tested. It is more patina than steel blackener; it contains black dye-oxides that are combined with acids to create a "transparent" black surface with rusted undertones. Here I steel-wooled back the surface to expose the patina color.
2) Patina Stain and Universal Black Patina are two finishes that utilize dye-oxides to color the steel sheets. Neither of them create a true patina. They do not oxidize the metal in any form; they simply lay on the surface of the steel. The Patina Stain is the concentrate, and the Universal Black Patina is a diluted form of the stain. Initially, the Universal Patina appeared to be an unstable finish; it wiped right off with a paper towel. However, with a coat of lacquer it held firm. The Patina Stain sample proved to be unstable with and without the lacquer.
Wax Sealants
The waxes tested in this project were acquired from two suppliers: Sculpt Nouveau and Art Research Enterprises (AR). The waxes tested from Sculpt Nouveau are formulated as final coat sealant waxes that can be applied cold or hot depending on preference. The Dark Wax from AR is specified for hot application; however, in this study it was applied cold, in an attempt to simplify the finishing process.
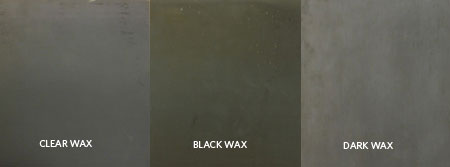
Sealants
3) The Clear Wax and Black Wax from Ron Young.
4) Dark Wax from AR which was developed as a hot wax metal sealant. Hot waxing is a process of sealing metal for exterior protection by heating the surface of the metal with a large propane torch and stippling the wax on to the metal surface with a brush or fine rag. The wax melts on contact with the hot metal and knits into the surface providing a durable layer of protection.
Clear Top Coats
Five different products were tested in this category for appearance, eco-friendliness, durability, and quality of touch-up refinishing. In selecting products, I focused on sealants that could easily be sprayed and that had a long pot life. This limited us to lacquers, paints, and urethane sealants. Each coating sample below is shown with an abrasion-repair test sample.
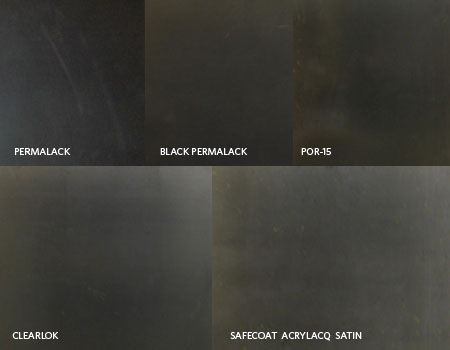
Top coats
5) Permalac and Black Permalac from Peacock Laboratories are high-performance lacquers developed for exterior metal application and are excellent for sealing bare metal surfaces. These lacquers are rated for ten years of exterior protection. Permalac VOC:778g/l, Black Permalac VOC:588g/l
6) POR-15 is a rust-preventative paint that is intended to be used to stop rust from continuing on already oxidized surfaces. It was chosen because of these properties and was the only product that was found for its intended use. VOC:236g/l. High viscosity made spraying this finish very difficult and resulted in a rough finish.
7) CLEARLOK is a water-based urethane sealant that is specified by the manufacturer as a rust-preventative coating for clean surfaces. Note the uneven finish. The finish was sprayed evenly and it moved as it dried.
8) Safecoat Acrylacq Satin is a water-based acrylic lacquer and was chosen because of its eco-friendly characteristics. VOC:120g/l. This finish re-oxidized the steel in places it had been previously.
Conclusion
After evaluating the results of all the finish tests and consulting with fabricators about the technical nuances of finish application, the decision was made to use Permalac Black for all structural steel extrusions in the Multifaith Center at Wellesley. We specified Permalac based on three principal factors: its visually subtle finish quality, and the consistency and ease of application. Further, by applying the Permalac in our shop, we could reduce the amount of toxic compounds used on the construction site.